Copper & Copper Alloy Melting
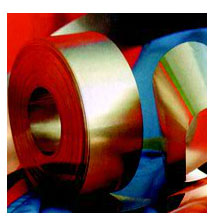
Copper, bronze and brass were melted with fuel-based furnaces until well into the 20th century, when the clear advantages of induction melting technology have made it the modern solution for melting these metals.
From removable crucible furnaces, used to melt just a few pounds of brass for custom castings, to an 80 metric ton tilting furnace, used to cast giant bronze ship propellers, Inductotherm builds furnaces and complete melt shop systems for virtually every copper and copper alloy application.
Copper finds use as a heat conductor, an electrical conductor, as a building material and has a significant presence as a decorative metal art. It can also be used as an anti-germ surface that can add to the anti-bacterial and antimicrobial features of buildings such as hospitals. With all of these available uses, its no wonder why copper was known to some of the oldest civilizations on record and has a history of use that is at least 10,000 years old.
Inductotherm is the leading manufacturer of induction melting and automated pouring systems used by companies worldwide to melt and cast copper and copper alloys. Induction technology has given copper and copper-based alloy producers and casters the ability to melt with precise metallurgical and temperature control, low metal loss, minimal gas pickup and an environmentally clean process.